The Comprehensive Automation System
The Driverless technology is an innovative system already used in the subways of Hong Kong, Lille, Paris, and especially Copenhagen, which has a configuration most similar to that adopted for the construction of Line C in Rome. In addition to Line C in Rome, the driverless system is used in Italy in the metro systems of Brescia and the new Line 5 of the Milan metro.
The Comprehensive Automation System replaces the role of the train operator, as it can: operate the vehicle, guide it on the track, control its departure/stop and speed, manage the opening/closing of platform doors, and detect obstacles and emergency situations. The train can perform various tasks autonomously, such as automatic in-line recovery, and more.
Furthermore, the vehicle has the ability to communicate in real-time with the control center, from which the operation of the line is managed almost entirely automatically (only major decisions or serious anomalies are handled by the personnel at the Central Control Center).
Each train has 52 passenger access points: messages/images can be exchanged in real-time between all vehicles in operation and the Control Center. Each vehicle is equipped with a complete audio and video information system, an SOS button for emergency situations, and an INFO button for receiving information.
Passengers can rely on constant monitoring carried out directly from the Operations Center; each train is equipped with 12 cameras and as many video monitors, so any service anomalies along the line or at stations are immediately reported. The audio system allows for real-time emergency announcements.
The initial order for Metro C to AnsaldoBreda includes 13 trains currently in operation on the line, each consisting of 6 carriages. The trains have 204 seats, with spaces for people with disabilities and for transporting bicycles. The cruising speed will be 35 km/h, but the trains can reach speeds of up to 80 km/h. They are 109.4 meters long, making them the largest Driverless high-automation trains in Europe.
Before the start-up, the Line C trains underwent a series of tests and trials. Functionality and safety tests were conducted on the international Velim circuit in the Czech Republic, where a prototype traveled over 20,000 kilometers.
At the Montelibretti Fire Brigade Center, a carriage underwent a fire test in an artificial tunnel to verify the resistance of materials and the exhaust of fumes produced by a potential fire in a stationary train at a station or in a tunnel.
To determine the thermal power curve, the behavior of materials, and the correct sizing of safety systems, an identical carriage/train was sacrificed in a unique experiment worldwide. This provided irrefutable data, allowing the entire international scientific community to acquire invaluable real-world data for better defining fire prevention strategies and passenger evacuation management in tunnels.
In light of this experiment, the vehicle produced not only complies but also exceeds the performance values set by the latest European regulations for fire prevention.
Key Subsystems
The main subsystems on which the driverless system is based are: ATC, Platform Screen Doors, Vehicle, Power Supply, Telecommunications, SCADA, Access Control and Fare Collection, Civil Facilities.
ATC (Automatic Train Control)
The ATC system manages the processes by which vehicle movements are controlled and regulated safely and efficiently, allowing trains to operate automatically without onboard staff, both along the line and in depot areas.
The automatic train operation system consists of three subsystems that have been tested individually for a long time in numerous railway infrastructures and subways:
– ATP (Automatic Train Protection) is an automatic protection system that controls the distance and speed between trains. Used since the beginning of the last century in the first subways, it ensures the safe operation of the transportation system, for example, by imposing a safe distance between trains, respecting speed limits on various sections, and safely loading passengers through the control of platform and vehicle doors.
– ATS (Automatic Train Supervision) is a global control system for the system and centralized traffic management. It manages train movements in relation to the established operational program.
– ATO (Automatic Train Operation) is an automatic driving system that regulates the train’s operation according to the instructions provided by the ATS system and stops at the target in stations. It also automatically controls train movements, from starting the route, stopping at the station, to automatically recovering a train in case of breakdown.
SCADA
The SCADA system – Supervisory Control and Data Acquisition – is capable of managing an enormous flow of information, certainly unique among all similar transport systems. Currently, with the opening of the line between Monte Compatri/Pantano–Lodi, there are 21 operational stations, with an average of about 7,500 communication points per station. From each individual point, a series of status messages are sent to the control center. This results in a total of over one million real-time exchanged pieces of information.
CCTV
In the tunnels, cameras are installed every 200 meters, as well as on platforms and in outdoor areas. An impressive transmission network based on Ethernet – Optical Fiber – WIFI allows information exchange and transmission to dozens of high-resolution, large screens at the Central Control Center, providing an accurate view of the entire line.
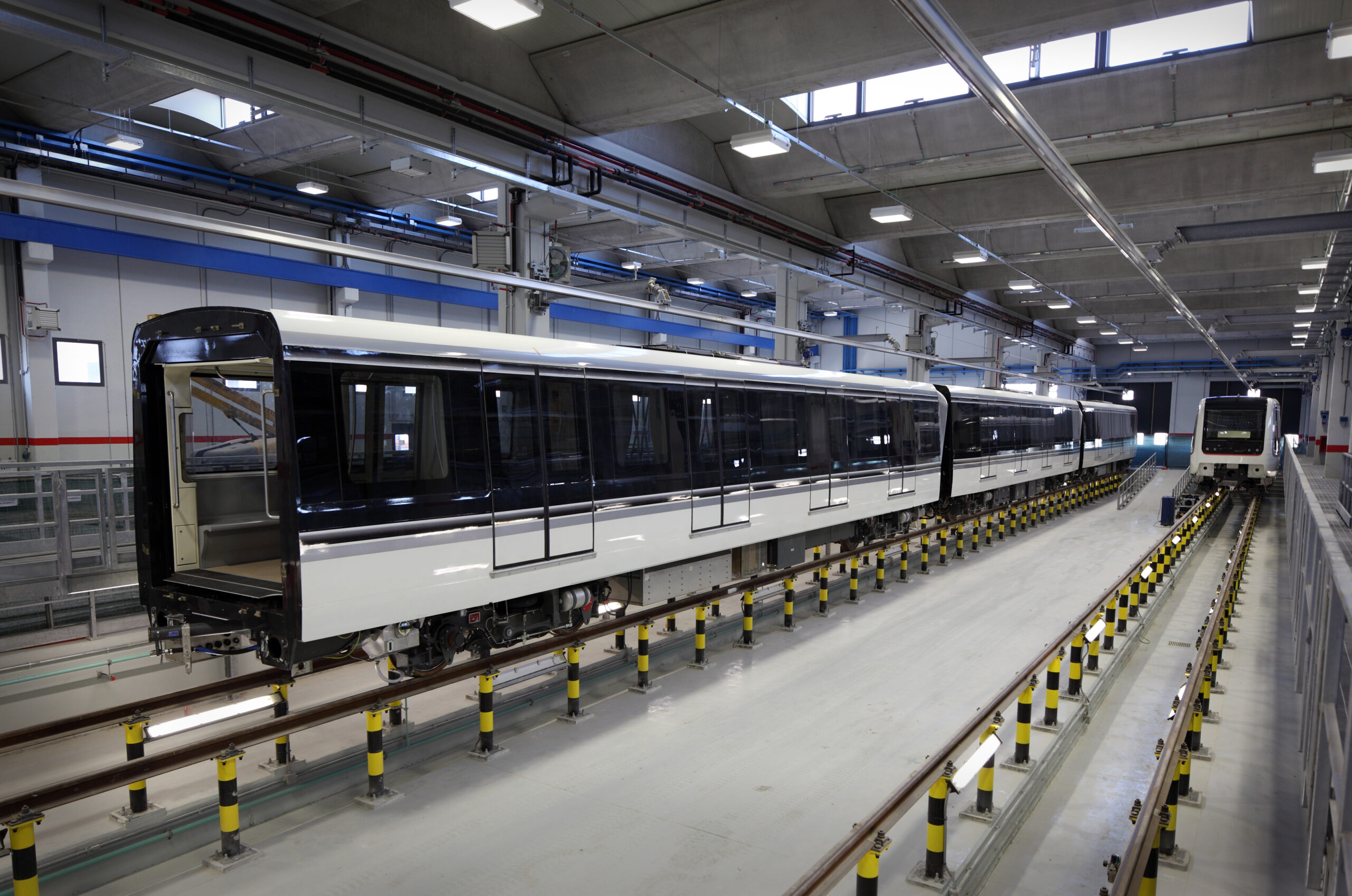
The Granite Depot Workshop and the Central Operations Center
The Granite Depot is located on a 20-hectare area and serves as the shelter for the entire fleet. It can accommodate 42 trains and is operated 90% automatically. The depot is equipped with parking areas, automated undercarriage washing and blowing zones, as well as preventive and corrective maintenance workshops.
At the heart of the depot lies the Central Operations Center, a control room similar to an airport’s, from which all operating trains are guided and monitored.
Main Functions:
- Train traffic control
- Passenger surveillance for security purposes
- Supervision and control of electric traction systems
- Communication with passengers on trains and platforms
- Communication with on-line service personnel
- Dissemination of information to passengers (audio-video)
- Audio-video recording
- Recording of events and significant operating data from all subsystems
Management Aid Systems
For Metro C, original and specific management aid systems have been developed to enhance the safety of handling a complex line.
ODSS
The Operational Decision Support System (ODSS) developed for Line C assists the operators of the driverless system in managing operational conditions, both during normal operation and in the event of anomalies. This system provides guidance on the correct actions to be taken and supports their efficient execution.
The support capabilities of ODSS are based on a knowledge base comprising the plant configuration, formalized operational procedures, and so-called “Action Cards,” which represent the formalized operational procedures in a concise manner. ODSS can be logically divided into three main environments, depending on the functionalities available to the user:
- Decision Support Environment;
- Maintenance Environment;
- Training Environment.
For each of these areas, the correct procedures to be implemented are presented to the operators.
DIAG
The Integrated Diagnostic System (DIAG) is an operational aid system dedicated to managing Line C.
DIAG functions by analyzing events aimed at diagnosing the system and primarily operates based on the information collected and made available through a tool (DAS) that normalizes received information. This enables integration and appropriate processing (through filtering/correlation). As a result, effective identification of equipment malfunctions, fault causes, and “faulty” components is possible. Correlations must take into account the temporal dimension to effectively achieve these objectives.
To perform its function, DIAG is equipped with tools for:
- Defining correlations;
- Executing correlations;
- Presenting diagnostics.
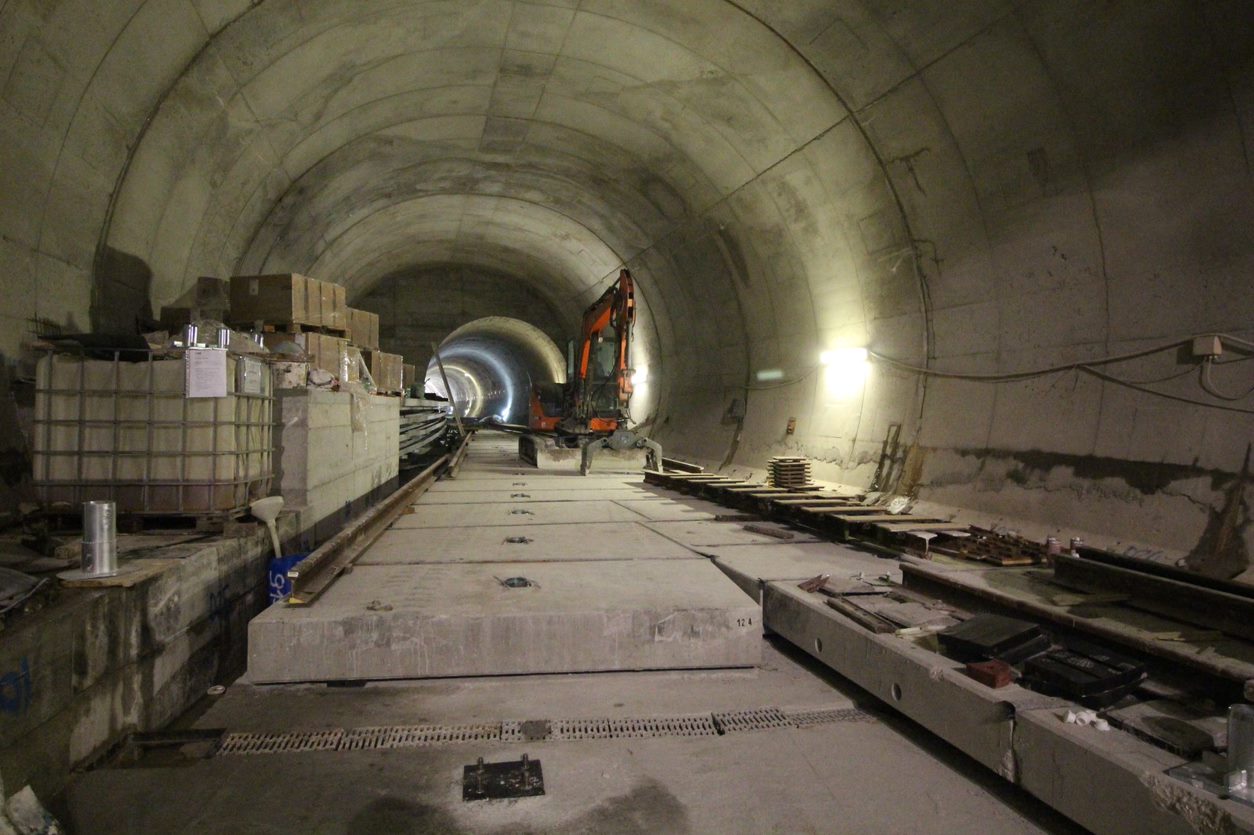
SGM – Maintenance Management System
The Maintenance Management System (SGM) is based on the Carl Source product (by Carl Software), which has been appropriately configured, equipped with certain add-ons, and complemented with ad hoc reporting. It also includes an interface module to the Normalization Layer. This system analyzes how the provided solution can meet the requirements matrix specifically developed for Metro C. The technical report, developed in conjunction with the technical documents related to the solution’s implementation, forms the basis for acceptance testing.
PIC – Performance Index Calculator System
The system, which acts as an interface between the central ATC and the Performance Index Calculator System, is simply referred to as PIC. It integrates data from the field to provide values for system Availability (D) and Punctuality (A) parameters.
In the development of PIC, security and privacy were taken into account. Access to the application is only granted after credential request and verification. Different user profiles are provided to ensure exclusive access to various product functionalities. PIC has been designed and developed to facilitate the interaction process between the system and the user. The user-friendly graphical interface allows the product to be used by individuals without specific computer knowledge.
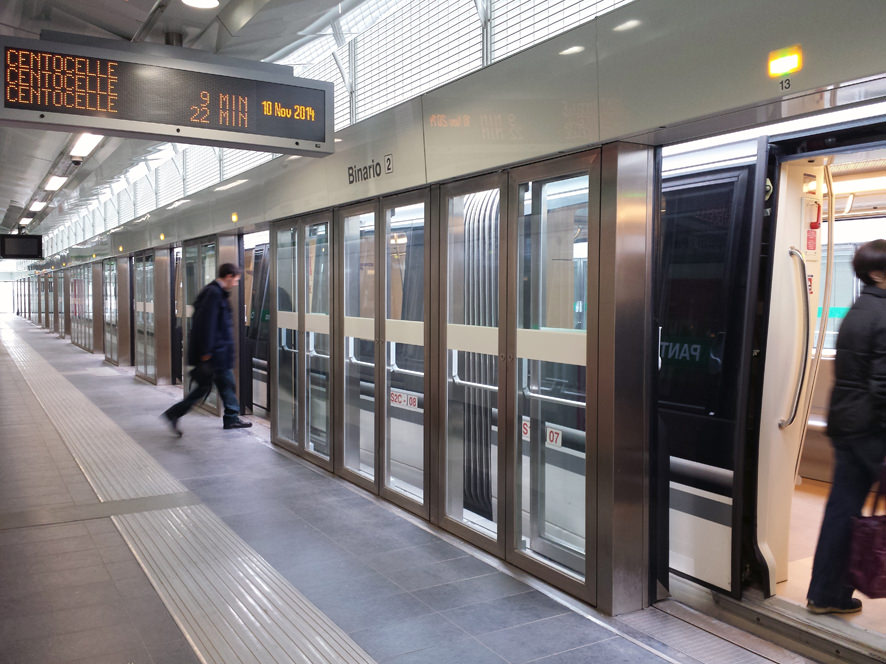
The system implemented for the “Performance Index Calculation” is designed to provide the necessary information to determine if the Rome Metro Line C is operating according to its schedule.
To fulfill this task, the PIC system calculates the following indicators:
- Overall Availability (DO): This parameter measures the ratio between the actual operating time, during which correct operation is ensured, and the scheduled operating time;
- Technical Availability (DT): Similar to DO but takes into account the intervals of unavailability that are actually necessary to restore a fault;
- Adherence (A) to the operating schedule.
The PIC system has two modes for calculating these indicators:
- On-Line: The Overall Availability (DO) and Adherence (A) indicators are automatically calculated during the operating hours. These values are not final as they are based on the calculation of a portion of the field data (those available up to the calculation moment);
- Off-Line: The indicators are calculated at the end of the daily operating hours using all the field data collected during the operation.
During online calculation, the Overall Availability (DO) and Adherence to the Operating Schedule (A) indicators are processed at regular intervals that can be configured by an operator with an administrator profile (e.g., every 5 minutes).
The calculation of the Technical Availability (DT) indicator occurs in manual mode, meaning it only happens after an operator issues the specific command. In particular, Technical Availability (DT) can only be obtained following the validation of unavailability intervals by an operator. The main functionalities of the system can be classified into:
- Acquisition Functionalities;
- Processing Functionalities;
- Consultation Functionalities;
- Validation Functionalities.
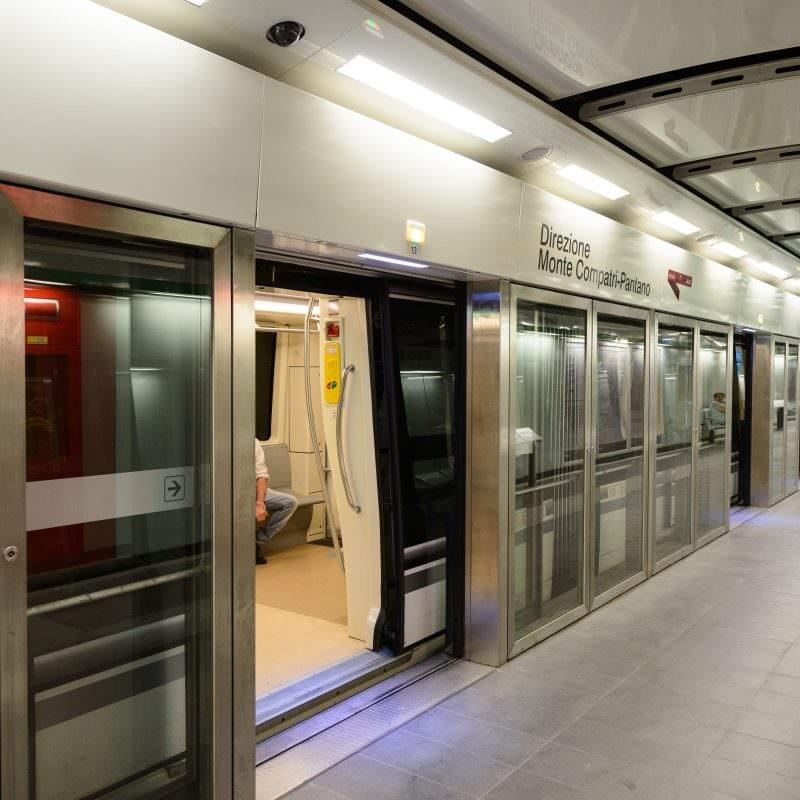